Since the LED is a sensitive semiconductor device and has a negative temperature characteristic, it is necessary to perform constant working conditions and shelter during the application process, thereby generating a driving concept. LED devices are almost demanding on drive power. LEDs are not like popular incandescent bulbs, and can be directly connected to 220V AC mains. The LED is a low voltage drive of 2 to 3 volts. It is necessary to design a complicated conversion circuit. LED lamps of different uses must be equipped with different power adapters. In the international market, foreign customers have very high requirements for the efficiency conversion, effective power, constant current accuracy, power supply life, and electromagnetic compatibility of the LED driver. To design a good power supply, these factors must be considered comprehensively, because the power supply is in all the lamps. The influence is as important as the human heart.
LED is a typical current-driven device that precisely controls the LED drive current and determines many parameters including light efficiency, power efficiency, heat dissipation and product brightness. Driving an LED is important to control its current. Whether it is directly increasing or decreasing the drive current, or the duty cycle (PWM) to reduce the switch-to-light ratio, it is the control current mode, but the target is not the same. This article will explain the differences between different drivers in different applications.
1, distributed constant current drive theory
In the past incandescent and energy-saving lamps market, it is difficult for LEDs to continue to comply with the mainstream lamp models with limited specifications. LEDs have the flexibility of application and will bring more power specifications in future designs.
The principle of distributed constant current is that independent constant current sources are set up at each parallel branch point to handle, maintain, control the intersection of the manifold and the manifold, the manifold and the whole line. The distributed constant current circuit can be regarded as a complete line structure in application, and the practical application is distributed in each node of the line, which is a circuit structure that can be controlled by the process LED constant current drive and can communicate with each other.
At present, there is a big gap between the spread of LED products and the actual application life. The invariance of the drive line will directly affect the overall product.
The reason why the distributed constant current technology has high reliability is that the AC power supply section continues to use the conventional switching power supply, and the constant voltage power supply mode is adopted. The accumulation of switching power supply technology will create moral conditions for LED power supply design. Under the same power supply specification, it is no longer necessary to develop new power supply models, the power can be backward compatible, greatly reducing power supply specifications and improving power supply identity.
2, the combination of soft and hard precision control ideas
In the daily drive power supply design, the cumulative error of peripheral devices is very difficult to handle, resulting in a far cry from the original design of the drive power parameters. The constant current drive requires current detection. The usual practice is to connect the millicouple resistors in the manifold to obtain feedback information. To achieve high efficiency, the resistance value will be smaller. Too small millicouple resistors will cause inconvenience to the production and testing. The general instrument can not verify the exact value, the process of the basin will also affect the accuracy, and the resistance mode set the current is a fixed mode, and the adjustment is not convenient.
The combination of software and hardware will open the Pentium of LED application technology. The LED constant current accuracy value is softwareized, which can greatly improve the flexibility of LED applications. Through the process of the computer to manipulate the software, the circuit current setting is completed with a straightforward digital write.
It is our goal to drive the zero components around the line. Peripheral zero devices do not introduce error in the design device parameters, which greatly improves the accuracy of the constant current.
China's IC manufacturing process can not meet the LED drive accuracy requirements, but we can use the new technology and new methods to achieve the world's top constant current accuracy. Driving precise control is one of the methods.
In the drive precision control, it is important to see what the design goal is to follow the highest light efficiency, or according to the consistency of the lamp design, if it is limited to the accuracy of the drive current, it is actually very easy to do. For example, the drive current is not accurate, or there is shelter with temperature changes. The customer requests that all parameters meet the requirements, such as product consistency, effectiveness, and so on.
For these requests from customers, we need to work hard on design. At the end of the day, how to control the accuracy, and ultimately adjust the current according to our design intent, improve the product's invariance.
The value is implemented. The built-in non-volatile E2PROM can be selected. Reliable to any register can fulfill its obligations, and the type of memory can be determined according to the conditions of use and process permission.
The division and design of the current levels can vary from market to market. There is always an error in the output current due to the manufacturing process, which will be improved after software.
When the driver IC of Changyuntong is delivered from the factory, it can supply different current output values ​​according to different needs of customers, eliminating the batch calibration process. Small-volume customers can also override the current value by the computer software that comes with the process.
3. New design method to improve the driving efficiency
It is possible to drive the LEDs in a single series with an AC power supply, but a single series is only a small part of the LED driver application, and most applications have parallel connections. In the case of parallel LED driving, the disparity LEDs in the overall constant current design do not necessarily operate in a constant current condition, and all product LED currents affect each other.
In high-current designers, such as LED street light design, designers will not directly connect multiple LEDs in parallel, because such danger will occur rapidly. On weekdays, the first constant voltage and then the DC constant current are completed. We know that the DC drive efficiency is under reasonable voltage and load conditions, so how to ensure the number of load LEDs or LEDs with temperature changes within a fair range, how flexible the customer is to change the number of LED drivers to solve the above problems need to design AC to DC constant The feedback mechanism of the flow, but this technical condition is not available until now.
----------------------------
Small connector, contains great wisdom - electronic enthusiasts in March "Connector Technology Special" free download!
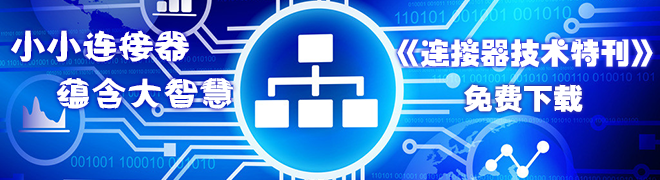
Reverse Conducting Thyristor(RCT)
Reverse Conducting Thyristor(RCT) is also called Reverse- appreciation Thyristor.The characteristic is that a diode is connected in reverse parallel between the anode and cathode of thyristor, so that the transmitting junction of anode and cathode is short-circuited.As a result of this special circuit structure, it has high voltage resistance, high temperature resistance, short turn-off time, low switching voltage and other good performance.For example, the turn-off time of the reverse thyristor is only a few microseconds, and the working frequency is dozens of KHZ, which is better than the fast thyristor (FSCR).This device is suitable for switching power supply and UPS uninterrupted power supply. One RCT can replace one thyristor and one continuous current diode respectively.
Reverse Conducting Thyristor,Original Reverse Conducting Thyristor,New Reverse Conducting Thyristor,Reverse-Conducting Thyristor 2200V
YANGZHOU POSITIONING TECH CO., LTD. , https://www.cnfudatech.com